How Smart Manufacturing is Changing the Molding Hose Industry
- Auto rbw
- Jan 30
- 4 min read
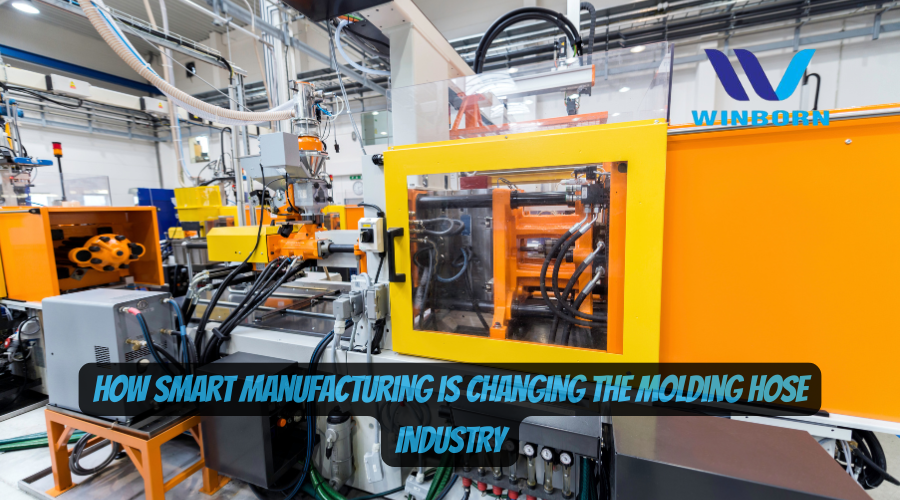
The molding hose industry is experiencing a technological revolution as smart manufacturing redefines production efficiency, quality assurance, and sustainability. Traditionally, molding hose manufacturers relied on manual operations, often leading to inconsistent product quality, high operational costs, and excessive material waste. However, with the rise of automation, real-time monitoring, predictive maintenance, and AI-driven analytics, manufacturers are now optimizing their molding processes for greater precision and efficiency.
As innovative factory technology becomes more prevalent, manufacturers leverage real-time data, digital twins, and AI-powered decision-making to streamline supply chains, reduce downtime, and improve product consistency. These innovations make molding hose production more cost-effective and sustainable, enabling companies to compete in a digital-first manufacturing landscape.
This article will explore how smart manufacturing technologies are revolutionizing molding hose manufacturer and shaping the future of industrial manufacturing.
The Evolution of Smart Manufacturing in the Molding Hose Industry
Traditional vs. Smart Manufacturing: Key Differences
Challenges of Traditional Manufacturing
Manual processes resulted in inconsistencies in product quality, leading to higher defect rates.
Inefficient material management caused excessive waste, increasing production costs.
Reactive maintenance strategies led to machine failures, resulting in unplanned downtime and delays.
Labor-intensive production lines were difficult to scale without significant cost increases.
Benefits of Smart Manufacturing
Automation reduces human errors, improving production speed and precision.
Real-time data analytics optimize process control, ensuring consistent quality standards.
Predictive maintenance prevents equipment failures, reducing downtime and repair costs.
AI-powered efficiency improvements minimize resource wastage and energy consumption.
Adoption of Smart Manufacturing in the Injection Molding Industry
Plastic processors are integrating digital transformation to enhance manufacturing process control and efficiency.
Smart factory investments are gaining traction across industries like automotive, medical device manufacturing, and heavy equipment production.
AI, robotics, and machine learning are redefining quality control, predictive maintenance, and supply chain optimization.
Key Technologies Driving Smart Manufacturing in Molding Hose Production
Automation and Robotics in the Molding Process
Robotic automation accelerates molding cycles, reduces labor dependency, and enhances product uniformity.
Automated injection molding machines maintain precise temperature and pressure levels, ensuring consistency in hose dimensions.
Smart factory software enables machine-to-machine communication, improving workflow coordination.
Artificial Intelligence and Machine Learning for Process Optimization
AI-powered analytics allow manufacturers to adjust production settings in real time based on historical and real-time data insights.
Machine learning models predict equipment failures before they occur, enabling proactive maintenance.
AI-driven quality control systems analyze the material flow and defect rates, making automated corrections during production.
Real-time monitoring and Predictive Maintenance
IoT-enabled sensors track machine performance, detecting inefficiencies early.
Predictive maintenance algorithms analyze historical equipment performance, alerting manufacturers to potential malfunctions.
Cloud-based monitoring systems provide real-time visibility into production metrics, optimizing supply chain coordination.
Digital Twins and Smart Factory Capabilities
Digital twins simulate production scenarios, helping manufacturers test new processes before physical implementation.
Machine vision technology enhances defect detection, improving quality assurance.
AI-driven predictive modeling refines molding parameters, reducing scrap rates and optimizing resource utilization.
How Smart Manufacturing is Enhancing Quality, Efficiency, and Sustainability
Improving Product Quality Through Smart Factory Technology
AI-powered quality control detects subtle defects, ensuring consistent product standards.
Automated inspection systems eliminate human error in quality checks, reducing defect rates.
Advanced material tracking ensures uniform plastic injection, improving hose durability and reliability.
Reducing Costs and Waste with Advanced Technologies
Smart supply chain management systems optimize material procurement, minimizing waste and inventory costs.
Energy-efficient equipment reduces power consumption, significantly cutting operational expenses.
Automated recycling systems repurpose scrap material, promoting sustainable manufacturing practices.
Sustainable Manufacturing in the Molding Hose Industry
Eco-friendly processes reduce plastic waste and carbon emissions, aligning with green manufacturing goals.
3D printing innovations enable low-waste prototyping, allowing companies to test product designs without excess material usage.
AI-driven energy optimization reduces factory power consumption, lowering overall environmental impact.
The Future of Smart Manufacturing in Molding Hose Production
Emerging Trends in the Injection Molding Industry
Blockchain for supply chain transparency ensures secure, tamper-proof production tracking.
The expanded use of 3D printing allows customized, high-precision mold designs.
AI and robotics innovations lead to fully automated smart factories, reducing reliance on manual labor.
Smart Manufacturing Investments in the Plastics Industry
Leading manufacturers invest heavily in AI, automation, and cloud-based production management.
Government-backed initiatives like SecureAmerica Institute are supporting digital transformation in industrial production.
Predictive analytics and real-time monitoring are becoming essential for cost-effective and efficient manufacturing.
How Molding Hose Manufacturers Can Stay Competitive
Leveraging AI-driven predictive maintenance to avoid unplanned downtime.
Implementing real-time analytics to optimize production workflows and reduce waste.
Adopting next-generation automation to improve efficiency and scalability.
Overcoming Challenges in Smart Manufacturing Implementation
Cost Barriers to Adoption
Smart manufacturing solutions require a significant upfront investment, but long-term cost savings outweigh initial expenses.
Government incentives and grants are available to support industrial automation initiatives.
Workforce Training and Skill Gaps
Implementing AI-driven processes requires a skilled workforce trained in innovative factory operations.
Manufacturers must invest in employee training to ensure seamless automation and digital technology integration.
Cybersecurity Risks in Smart Factories
Increased reliance on IoT-connected devices exposes manufacturers to cyber threats.
Strong cybersecurity frameworks and real-time monitoring systems are necessary to protect production data.
Conclusion
The molding hose industry is evolving rapidly with the integration of innovative manufacturing technologies. Manufacturers can significantly enhance product quality, reduce costs, and improve operational efficiency by leveraging AI, real-time monitoring, automation, and predictive maintenance.
As digital transformation continues, companies must embrace advanced manufacturing technologies to stay competitive in the global market. Those who invest in innovative factory solutions will benefit from reduced waste, lower operational costs, and superior quality control, ensuring long-term sustainability and profitability.
With the continued adoption of AI, robotics, and data-driven process optimization, molding hose manufacturers will pave the way for the future of efficient, high-quality, and environmentally responsible production.
Commentaires