Understanding the Materials Used in Hose Molding
- Auto rbw
- Jan 20
- 4 min read
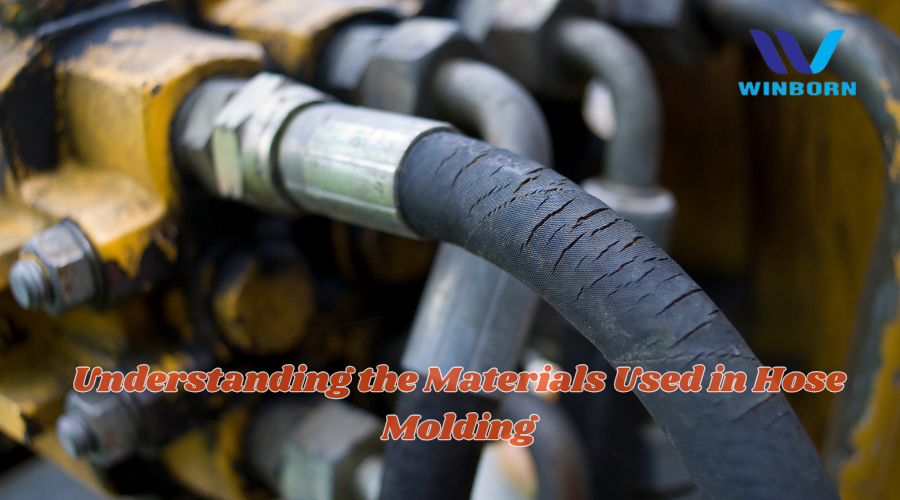
Selecting the right materials for hose molding is critical to ensuring durability, safety, and efficiency across various industries. From industrial machinery to automotive applications and even medical settings, hoses serve vital roles. Their performance often hinges on the materials chosen during the molding process. This blog explores the materials used in hose molding, why they matter, and how a trusted molding hose manufacturer can make all the difference.
Why Hose Molding Matters Across Industries
Hose molding is the process of shaping materials into flexible and durable tubes that transport liquids, gases, or other substances. Whether it’s hydraulic systems, fuel lines, or medical tubing, molded hoses are indispensable.
The material used in hose molding directly impacts a hose's performance. The material determines flexibility, resistance to environmental factors, and longevity. Poor material choices can lead to frequent breakdowns, safety hazards, and increased costs, emphasizing the need for reliable solutions from an expert molding hose manufacturer.
Why Material Choice Matters in Hose Molding
Key Factors Influencing Material Selection
Flexibility and Elasticity: Some applications demand hoses that bend and stretch without cracking or losing shape.
Resistance to Chemicals and Temperature: Industrial hoses often carry corrosive liquids or operate in extreme temperatures, requiring highly resistant materials.
Durability and Cost-Efficiency: Selecting the right material ensures longevity and minimizes the total cost of ownership.
Application-Specific Needs: Medical hoses prioritize biocompatibility, while automotive hoses require heat and fuel resistance.
Consequences of Poor Material Choices
When the wrong material is used, hoses may fail prematurely. This can lead to system malfunctions, safety risks, and costly repairs. A trusted molding hose manufacturer not only provides high-quality materials but also offers expertise in tailoring products to meet specific requirements.
Common Materials Used in Hose Molding
Natural Rubber (NR)
Natural rubber is known for its flexibility and excellent tensile strength. It works well in applications requiring vibration absorption. However, it’s less resistant to chemicals and heat, limiting its use in high-stress environments.
Synthetic Rubber Types
EPDM (Ethylene Propylene Diene Monomer):
Resistant to heat, ozone, and UV exposure.
Ideal for outdoor and automotive applications.
NBR (Nitrile Rubber)
Known for its oil and fuel resistance.
Commonly used in automotive fuel lines and industrial applications.
Silicone Rubber
Withstands high temperatures and remains flexible.
Often used in medical and food-grade hoses.
Neoprene
Offers resistance to weather, abrasion, and moderate chemicals.
Suited for outdoor applications and machinery.
Plastic Materials
PVC (Polyvinyl Chloride)
Lightweight and cost-effective.
Common in water hoses and low-pressure applications.
Polyurethane (PU)
Combines abrasion resistance with excellent flexibility.
Widely used in pneumatic hoses.
Composite Materials
Composite materials blend the advantages of rubber, plastic, and other substances to meet specialized needs. They are often used in heavy-duty applications where durability and resistance to multiple factors are crucial.
Material Properties to Consider for Different Applications
Industrial Hoses
Materials must withstand high pressure, chemical exposure, and wear and tear for industrial purposes. EPDM and NBR are popular choices due to their resilience and resistance.
Automotive Hoses
Automotive hoses require materials that can handle fuel, oil, and extreme temperatures. Silicone and NBR are often preferred for their performance in such conditions.
Medical Hoses
In the medical field, hoses must meet strict safety and health regulations. Silicone is preferred for its biocompatibility, sterilization properties, and flexibility.
The Role of a Molding Hose Manufacturer
Tailored Solutions for Diverse Needs
A leading molding hose manufacturer doesn’t just produce hoses; they collaborate with clients to develop solutions tailored to specific applications. This includes selecting materials that meet performance and regulatory standards.
Innovations in Material Technology
The best manufacturers invest in research and development to create new materials that enhance performance. For instance, advancements in composite materials now provide unmatched durability and flexibility for high-stress environments.
Ensuring Consistency and Quality
Top manufacturers use rigorous testing and quality control measures to ensure each hose meets the required standards. Businesses can minimize risks and improve operational efficiency by partnering with a trusted molding hose manufacturer.
Environmental Considerations in Hose Molding Materials
As industries move toward sustainability, eco-friendly materials are gaining traction.
Recyclable Materials: Some manufacturers now offer hoses made from recyclable plastics and rubbers.
Reduced Environmental Impact: Innovations like biodegradable materials are becoming more prevalent.
Sustainable Manufacturing Practices: Leading molding hose manufacturers adopt greener production processes, reducing waste and energy consumption.
Choosing a manufacturer committed to sustainability benefits the environment and aligns with consumer demand for responsible practices.
FAQs:
1. What is the most durable material for industrial hoses?
EPDM and composite materials are among the most durable due to their resistance to extreme conditions and wear.
2. How do I choose the right material for my hose application?
Consider factors such as the operating environment, pressure, temperature, and the type of substance being transported. A reliable molding hose manufacturer can provide expert guidance.
3. Are there eco-friendly options for hose molding materials?
Yes, many manufacturers now offer hoses made from recyclable or biodegradable materials.
4. What testing standards are used to ensure material quality?
Typical standards include ISO certifications, pressure and temperature tests, and chemical resistance assessments.
5. How does a molding hose manufacturer ensure consistency in material performance?
Manufacturers maintain consistency through stringent quality control processes, advanced machinery, and continuous material testing.
Conclusion
Understanding the materials used in hose molding is essential for selecting the right product for your needs. The choice of material affects a hose's flexibility, durability, and overall performance. Businesses can access tailored solutions that deliver reliability and efficiency by working with a trusted molding hose manufacturer.
Whether in the industrial, automotive, or medical sector, choosing the right materials and manufacturer ensures your operations run smoothly. For expert advice and high-quality hoses, consult a reputable molding hose manufacturer today!
תגובות