What Is the Manufacturing Process Behind High-Quality Molding Hoses?
- Auto rbw
- Jan 29
- 5 min read
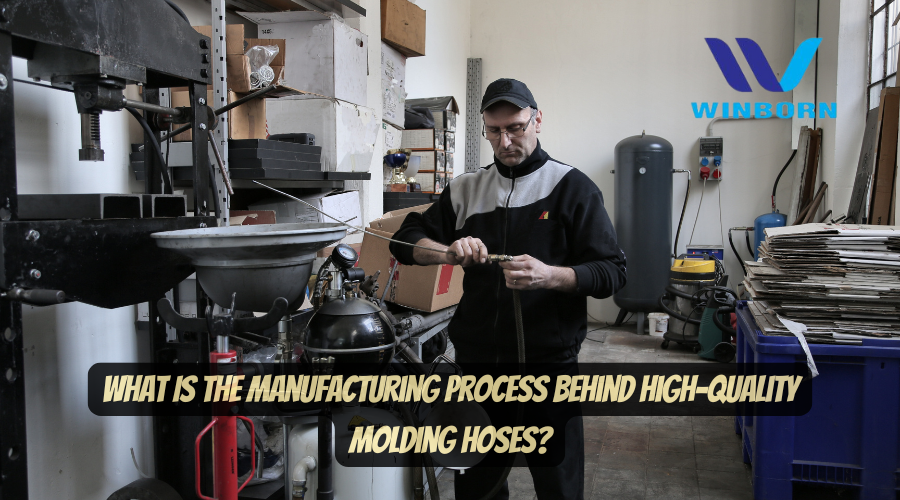
Molding hoses are crucial in various industries, offering solutions for high-pressure systems, fluid transport, and more. Molding hose manufacturers use advanced molding techniques, such as compression and injection molding, to produce durable, flexible, and high-performing hoses. In this blog, we’ll walk you through the manufacturing process behind these high-quality hoses, from design to final testing, focusing on the importance of material selection, molding processes, and precision in achieving the best results.
Why High-Quality Molding Hoses Are Important
High-performance molding hoses are critical in the automotive, medical, and industrial sectors, where performance and reliability are paramount. These hoses must be manufactured to withstand extreme conditions, whether used for transporting fluids, managing high-pressure systems, or ensuring cooling efficiency.
A molding hose manufacturer incorporates advanced molding techniques and high-quality materials to produce hoses that meet the industry’s stringent standards for durability, strength, and precision.
Materials: The Foundation of High-Quality Molding Hoses
At the core of any high-quality molding hose is the material selection. The most commonly used materials are rubber compounds, which offer the flexibility, strength, and resistance required for hoses to perform under demanding conditions. Synthetic rubber is often chosen for its resilience and pressure resistance, making it ideal for high-performance hoses.
Reinforcement Materials for Strength
Reinforcement layers are added to ensure hoses endure high pressures and harsh environments. These layers, often made from steel wires, fibers, or textiles, provide added strength and durability. A reinforcement layer is essential in high-pressure applications where the hose must withstand immense stress.
Selecting the Right Material for Specific Applications
The choice of material impacts the hose’s performance, and a skilled molding hose manufacturer carefully considers the application’s needs. For instance, medical hoses may require specific biocompatible materials, while industrial hoses may need materials that offer higher resistance to chemicals and heat.
Step 1: Designing the Mold and Selecting the Right Process
Importance of Mold Design in Molding Hose Manufacturing
Mold design is the first step in producing high-quality hoses. The mold cavity—the space inside the mold where the material is shaped—must be designed precisely to ensure consistent hose quality. The mold's design directly influences the hose's performance, strength, and durability.
Choosing the Right Molding Process
The next critical decision is selecting the correct molding process. Compression molding, injection molding, and transfer molding are the most common techniques molding hose manufacturers use. Each process has benefits, depending on the hose's complexity and volume.
Step 2: Rubber Molding Process – Injection vs. Compression Molding
How Injection Molding Works
Injection molding is commonly used when creating hoses that require high precision and complex designs. In this process, molten rubber is injected into a mold cavity under high pressure. This ensures the rubber fills the mold and shapes the desired hose. This method is ideal for mass production and creating hoses with tight tolerances.
Compression Molding for Mass Production
On the other hand, compression molding involves placing a rubber compound into an open mold cavity, where heat and pressure are applied to form the hose. This technique is especially suited for producing simple-shaped hoses in high-volume production runs.
Step 3: Reinforcement and Layering Techniques
Importance of Reinforcement Layers
Reinforcement layers are essential for hoses that withstand high pressure or abrasive conditions. These layers are typically added between the inner tube and outer cover of the hose to enhance its overall strength and durability. Common reinforcement materials include textile fabrics, steel wires, and braided fibers, all designed to boost the hose ability to perform under extreme pressure.
How BMC Reinforcement Enhances Hose Performance
BMC (Bulk Molding Compound) is sometimes used in specialized applications to increase a hose’s performance. This reinforcement layer can be used to ensure that the hose can withstand even more challenging conditions, such as high heat or pressure in industrial settings.
Step 4: Curing and Vulcanization
What Is Vulcanization?
The final molding stage is curing or vulcanization, a chemical process that hardens the rubber compound and creates cross-links between the rubber molecules. This process is crucial for achieving the final product's desired flexibility, strength, and durability.
Vulcanization allows the molded rubber to maintain its integrity, ensuring the hose can withstand extreme pressure and temperature fluctuations while remaining flexible and functional.
The Role of Heat in Vulcanization
Heat is applied during vulcanization, which causes the rubber to form cross-linked bonds that enhance its overall strength and performance. Without vulcanization, the hose would be too weak and would not have the required durability for high-stress applications.
Step 5: Quality Control and Testing
Rigorous Testing for Performance Assurance
They undergo rigorous quality control tests to ensure molding hoses meet the necessary standards. Some common tests include:
Pressure resistance testing ensures the hose can withstand the required pressure without failing.
Material strength testing to verify the hose's ability to endure physical stress.
Flexibility testing to check the hose’s ability to bend and move without cracking or breaking.
These tests guarantee that the molded rubber hoses meet industry standards and perform reliably in their intended applications.
Ensuring Consistent Quality in Mass Production
A skilled molding hose manufacturer will implement quality control throughout the manufacturing process, from the initial material selection to the final product inspection. This ensures that every hose produced maintains the same high resistance, flexibility, and durability standards.
Applications of High-Quality Molding Hoses Across Industries
Automotive Industry Applications
In the automotive industry, molded hoses are used in various systems, including air conditioning, cooling, and exhaust systems. Molding hose manufacturers produce durable hoses to handle the extreme temperatures and pressures in automotive environments.
Medical Device Applications
In the medical sector, molded rubber hoses are used in fluid delivery systems, medical equipment, and more. These hoses must meet strict standards for biocompatibility and safety, ensuring reliable performance in sensitive environments.
Industrial Applications
Industrial hoses are crucial in fluid transport, air conditioning, and high-pressure systems. High-quality molded rubber hoses are vital in these applications, offering the strength and resistance needed for demanding industrial environments.
Advantages of Partnering with a Reliable Molding Hose Manufacturer
Ensuring Consistent Quality
Partnering with an experienced molding hose manufacturer ensures your business receives consistently high-quality products. Experienced manufacturers use state-of-the-art molding processes, like injection molding and compression molding, to produce hoses that meet your exact specifications.
Expertise in Material Selection and Mold Design
A reliable manufacturer also has the expertise to guide you through material selection, ensuring that the right rubber compound and reinforcement layer are chosen to meet your specific needs. Their in-depth knowledge of mold design and molding processes ensures that every hose is produced to meet the highest standards.
Conclusion
Understanding the manufacturing process behind high-quality molding hoses is essential for businesses seeking reliable, durable, high-performance hoses. From material selection to vulcanization and quality control, every process step contributes to the final product’s strength, flexibility, and resistance. Working with a reputable molding hose manufacturer guarantees to receive a product that meets industry standards and performs reliably in your application. Whether for automotive, medical, or industrial use, high-quality molded hoses are essential to maintaining optimal performance and longevity in your systems.
Comments