Why Would Turbo Hose Keep Blowing Off?
- Auto rbw
- Jan 15
- 6 min read
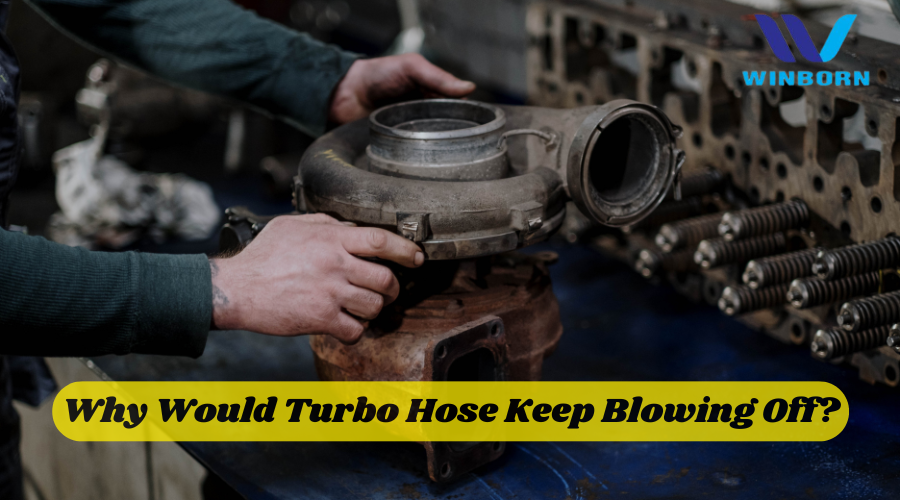
Turbo hose failures frustrate automotive professionals and enthusiasts, particularly with high-performance vehicles. Imagine accelerating in a sports car, feeling the turbo engine surge, only for the power to suddenly drop. You pull over, pop the hood, and find the turbo hose blown off. Understanding turbo hose blow-offs and prevention is vital. Turbo hoses deliver compressed air from the turbocharger to the engine’s intake system. A blown hose causes power loss, reduced performance, and potential damage. This blog explores why turbo hoses fail, prevention methods, and how selecting the right Turbo Hose Supplier can enhance your engine’s performance and longevity.
The Role of Turbo Hoses in Engine Performance
Turbo hoses are integral to the performance of turbocharged engines. These hoses transfer the compressed air generated by the turbocharger into the engine's intake manifold. This air boost increases the engine's oxygen supply, resulting in more efficient combustion, enhanced power output, and improved fuel efficiency. Without the proper turbo hose, even the most well-tuned engine can suffer from power loss, excessive heat buildup, or poor air-fuel ratios.
In modern performance vehicles, turbo hoses have evolved from simple rubber tubing to highly engineered components made of specialized materials that can withstand the extreme conditions of a turbocharged system. Whether you're in a sports car, a heavy-duty truck, or an industrial machine, the turbo hose's ability to handle high temperatures and pressures directly impacts the overall performance and reliability of the engine.
The Science Behind Boost Pressure
Boost pressure refers to the increased air pressure delivered to the engine via the turbocharger. This allows the engine to burn more fuel and produce more power. However, with increased pressure comes increased risk. As boost pressure rises, so does the stress on the turbo system and, notably, the turbo hose.
Managing Turbo Hose Pressure Spikes
Pressure spikes, often caused by rapid throttle application, aggressive driving, or modifications to the turbo system, can lead to sudden surges of force that the hose cannot handle. When the turbo hose is subjected to these spikes without sufficient strength or proper sealing, it can blow off, causing a significant loss of power and potentially damaging the surrounding components.
Key Factors in Preventing Blow-Offs
Understanding how boost pressure works and the stress it places on turbo hoses is crucial for addressing the root causes of blow-offs. Keeping pressure levels within the hose’s rated capacity and using quality materials to resist such stresses will help prevent failures.
Why Turbo Hoses Blow Off?
As engines are modified for performance, it’s not uncommon for drivers to increase the boost pressure to extract more power from the turbocharger. However, this modification can quickly backfire if the turbo hoses aren’t designed to handle such excessive force.
Major Cause of Damage
Excessive boost pressure can lead to turbo hoses blowing off at high RPMs, especially if they are poorly secured or made from inferior materials. For example, a car owner might increase the boost pressure for better acceleration, only to find that the turbo hose can’t withstand the pressure, causing it to detach.
Issues Encountered with Upgraded Turbo Systems
Case studies of high-performance vehicles with upgraded turbo systems often showcase these issues. Performance shops and enthusiasts alike have experienced turbo hose blow-offs after making modifications without considering the importance of reinforced hoses and proper clamping solutions.
Clamping Solutions
The clamps used to secure turbo hoses to their respective components are just as crucial as the hoses. Even the best turbo hose is prone to failure without a strong, reliable clamp. T-bolt clamps, for instance, offer superior gripping force compared to worm gear clamps, making them the preferred choice for high-pressure applications.
T-Bolt Clamps vs. Worm Gear Clamps:
Many turbo hose suppliers recommend T-bolt clamps for their ability to provide an even because they cross the entire circumference of the hose. This ensures the hose stays secure, even during pressure spikes. Worm gear clamps, on the other hand, tend to focus on a smaller area, which can lead to slippage or weak seals over time.
Expert Advice
Experts in the field advise that proper clamping is essential for preventing turbo hose blow-offs. A clamp rated for high pressure and designed for the hose material ensures a more secure connection.
Material Matters: The Importance of Hose Composition
Not all turbo hoses are created equal. The material composition is significant in their durability and ability to withstand extreme conditions. Various materials, including silicone, rubber, and reinforced composites, are commonly used for turbo hoses.
Silicone hoses are known for their excellent heat resistance and flexibility, making them ideal for high-temperature applications.
Rubber hoses, while more affordable, often lack the temperature tolerance required for high-performance engines.
Reinforced composite hoses offer the best of both worlds, providing strength, heat resistance, and durability in extreme conditions.
Choosing the right material is essential for ensuring that your turbo hose can handle the pressures and temperatures of a turbocharged engine. A trusted Turbo Hose Supplier will guide you in selecting the right material based on your specific needs, whether you’re looking for flexibility, heat resistance, or durability.
Installation Errors: The Human Factor
Sometimes, turbo hose blow-offs are caused by installation errors rather than product failure. Incorrectly fitted hoses, improperly tightened clamps, or mismatched components can lead to premature hose detachment.
Common installation mistakes include:
Over-tightening or under-tightening hose clamps can damage the hose or fail to create a tight seal.
Installing a hose that’s too long or too short for the system causes unnecessary stress on the hose.
Not correctly cleaning the mating surfaces before installation can lead to leaks or weak connections.
These errors can all be prevented by paying attention to detail and following manufacturer instructions. Industry experts recommend hiring a professional to handle turbo hose installations, particularly for high-performance vehicles where precision is key.
Proactive Strategies: Ensuring Turbo Hose Reliability
Preventing turbo hose blow-offs starts with regular maintenance. Routine inspections should include checking the condition of the hoses for signs of wear and tear, such as cracks, soft spots, or bulging.
Maintaining a regular inspection schedule—typically every 10,000 to 20,000 miles—can help identify issues before they become critical. In addition to visual inspections, check the clamps to ensure they are still tight and that there’s no evidence of slippage.
Upgrading to High-Performance Components
One of the most effective ways to prevent blow-offs is to upgrade to higher-quality turbo hoses and clamps. Premium hoses made from reinforced silicone or composite materials provide superior performance and resistance to high temperatures, pressure, and aging.
Why Partnering with a Reputable Turbo Hose Supplier
Choosing a reputable Turbo Hose Supplier for these upgrades ensures that you invest in products that last longer and perform better under extreme conditions. A good supplier will offer various products suitable for multiple applications, from street vehicles to racing engines.
Leveraging Technology for Monitoring
Modern turbocharged systems are becoming increasingly sophisticated. Digital sensors and monitoring systems are now available to help track key variables such as boost pressure and air intake temperatures.
Installing a boost pressure gauge or an electronic monitoring system can help identify sudden pressure spikes or fluctuations, giving you the information needed to address issues before they cause hose failures.
Real-World Solutions from Turbo Hose Suppliers
Leading turbo hose suppliers are at the forefront of innovation in hose design, continually improving materials, construction methods, and performance features. Turbo hoses now incorporate new technologies such as multi-layered hose construction and heat-resistant coatings to provide additional durability and reliability.
Suppliers also focus on custom solutions tailored to specific engine types, offering performance hoses that can handle extreme conditions while maintaining flexibility and strength.
Troubleshooting Guide: What to Do When a Hose Blows Off
If your turbo hose blows off, it’s essential to act quickly:
Step 1: Safely pull over to the side of the road and turn off the engine.
Step 2: Let the engine cool down before inspecting the turbo hose and surrounding components.
Step 3: Look for visible damage, loose clamps, or other issues that could have caused the blow-off.
Step 4: Reattach the hose and secure it with the proper clamps, or replace the hose if necessary.
Long-Term Solutions: Preventing Recurrence
Invest in higher-quality hoses, ensure proper installation, and maintain regular inspections to prevent future turbo hose blow-offs. Also, consider upgrading to components designed to handle higher boost pressures and extreme temperatures.
Conclusion
Turbo hose failures can be frustrating but often preventable with the right approach. Understanding the causes—excessive boost pressure, poor clamping, inferior materials, and installation errors—can help you avoid common pitfalls. Investing in high-quality hoses and clamps, performing regular maintenance, and leveraging modern monitoring systems ensures your turbocharged engine performs at its best.
Comments